Cooling Towers: What They Are, How They Work, How to Maintain Them
All industrial facilities, as well as those for air conditioning or refrigeration or energy production are characterised by heat emissions: these are more or less significant in quantitative terms. Usually this “residual” heat has a low energy content that does not make its recovery possible or worthwhile. Therefore it must somehow be dissipated externally.
Among the various solutions available for this purpose, in this article we will be looking at cooling towers: they are recognised today as among the most efficient technologies available on the market.
by Giorgio Lorenzetti, Technical Advisor at MITA Cooling Technologies
1. Evaporative cooling towers: definition and working principles
The section below will attempt to answer the following most frequently asked questions.
- “What are evaporative cooling towers (or simply cooling Towers), what do they do and how do they work?”
- “Where are they used, and why? Why are they necessary?”
- “What is the definition of ‘cooling tower’ or ‘evaporative cooling tower’?”
- “What does ‘evaporative’ mean?”
1.1. What are Cooling Towers?
Evaporative cooling towers, or cooling towers are devices which make use of a natural principle which is as simple as it is effective: the forced evaporation of a minimum quantity of water, compared to the main mass, takes place by the dissipation of heat from the mass itself; the mass, therefore, cools down (latent heat of evaporation).
The process by which evaporative cooling occurs is as simple as it is ancient: the archaic amphorae made of terracotta, a porous material, allowed the water to leach outwards in minimal quantities. In this way, an evaporative process took place: the water inside was kept cool even in high ambient temperatures.
1.2. How do Cooling Towers work? Exploiting the latent heat of evaporation
Evaporative cooling towers are able to best realise the water/air heat exchange process: evaporation is forced through the use of simple, effective components which normally require minimum maintenance.
To better understand how heat dissipation occurs, two concepts need to be introduced.
- Sensible heat. This is the amount of heat energy that is added to, or subtracted from, a physical element (such as louvers) to change its temperature.
- Latent heat. This is basically founded on the change of state that a substance can undergo as a result of heat addition or loss. In the case of water, it can change from a liquid phase to a solid phase (ice) if heat is removed when it reaches freezing point. It can also change from a liquid phase to a gaseous phase (vapour) if heat is added when it reaches boiling point. Latent heat is therefore defined as heat that is introduced or removed to change the state of the water. Specifically, in evaporative cooling systems, it is defined as latent heat of evaporation.
A well-designed evaporative tower is able to provide the water with as much air contact surface area as possible, in order to optimise the latent heat exchange.
To make this heat exchange possible, the evaporative tower must therefore be able to offer a very high air/water contact surface. This is achieved by means of a heat exchange surface, specifically designed for the purpose, and a fan able to move a defined volume of air according to precisely defined parameters. We will now look at the importance of these internal components in detail.
1.3. The wet bulb temperature
An important physical concept makes it possible to have a better understanding of how cooling towers work: the wet bulb temperature is fundamental to the theory of how all evaporative systems and, more specifically, cooling towers work.
Practically speaking, this parameter precisely defines the “worst” conditions of temperature and relative humidity in the area of installation. It provides a precise reference for theoretically achievable output temperature of the evaporative tower.
1.4. Efficiency of cooling towers
Given their simple construction, combined with the high levels of efficiency in terms of cost/dissipated kW ratio, evaporative cooling towers are still the most commonly used cooling device in both HVAC and, above all, industrial environments: there are no particular moving parts, except a fan (which can be positioned at both the suction and delivery points). On the other hand, electricity use is truly low when compared to other systems used for the same purposes.
This is especially true where large heat amounts need to be dissipated (e.g. steelworks, chemical plants, power plants) as cooling towers are unrivalled in terms of the electrical power used and the minimum space required for their installation.
Not to mention that the achievable temperatures, with regard to cooled water, are well below the ambient temperature: unlike louver systems, for example, which are bound by this limit. This is due to the fact that the evaporative systems work by exploiting the latent heat of evaporation (the minimum achievable limit of the water is the wet bulb temperature).
1.5. A comparison of cooling technologies: evaporative, dry, adiabatic and mechanical coolers
When a cooling system for industrial processes or HVAC is to be built, several fundamental points must be considered: as a result, we ca select the most suitable system for our plant. Specifically, the decision must take into account both the required operating temperatures and the environmental conditions at the site of installation.
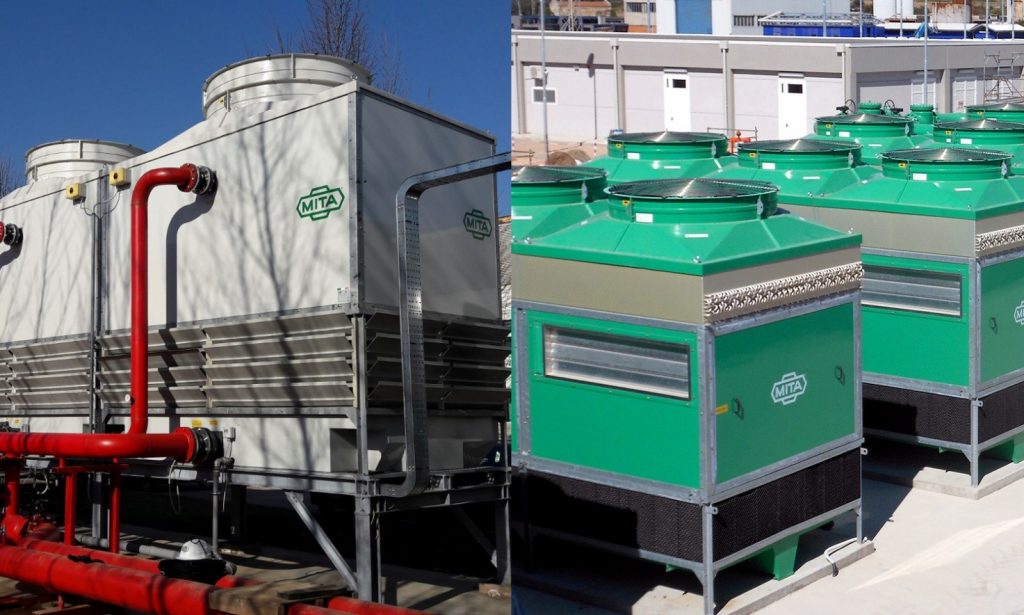
For example, if a temperature of the cooled fluid below ambient temperature is required, an evaporative system would be preferable: in this case, the minimum theoretical limit of the cooled fluid is, as we have seen, the wet bulb temperature of the air.
On the other hand, dry cooling systems are based on the sensible exchange which is much less efficient than the exchange of latent heat of evaporisation. The limit in this case is imposed by the temperature of the cooling fluid, namely the ambient air. Where it is sufficient to cool the fluid to a temperature above ambient temperature, an air cooler should be used.
A third option is to design an adiabatic system where a fluid temperature equal to or slightly lower than the ambient temperature is desired.
All this helps to show that there is no such thing as a “good for every season” cooling system: making the right choice, based on the design requirements and environmental conditions, means optimising energy use, reducing the required space and ensuring the systems are in conditions where they can operate at their best.
Chiller units are a separate subject: in this case, however, we are talking about devices that use specific mechanical components to achieve cooling (compressors, evaporators), instead of “natural” elements such as air or water.
Find out the comparative advantages of evaporative and adiabatic cooling2. Cooling towers: sizing and components
We have learned what evaporative towers are and the (simple) physical principle they use to maintain high performance.
We will now look at how they are built and, more specifically, the criteria used to determine their size.
2.1. How to size a tower: the importance of the wet bulb temperature
The size of an evaporative cooling tower is determined by a few fundamental parameters. These include:
- the thermal power to be dissipated;
- the temperature of the water entering the tower;
- the output temperature to be achieved;
- the thermo-hygrometric conditions (i.e. temperature and humidity) of the installation area.
This information especially is a decisive factor in determining the correct size. It makes it possible to identify that exact parameter of the wet bulb temperature which, as we have seen, defines the “worst” environmental conditions in the place of installation and the minimum temperature that the water cooled by the evaporative tower is likely to achieve.
In these conditions-limits, the project temperatures required to dissipate the thermal load supplied by the system must be guaranteed. Once the reference wet bulb temperature is determined (on average about 10°C lower than ambient temperature), it is clear that the approach required for the outlet water will be smaller and the evaporative tower required to achieve it will be larger. For “approach”, we mean the difference between the wet bulb temperature and the cooled water temperature.
Usually, an approach of between 2-3°C and 5-6°C fully meets the needs of most modern facilities.
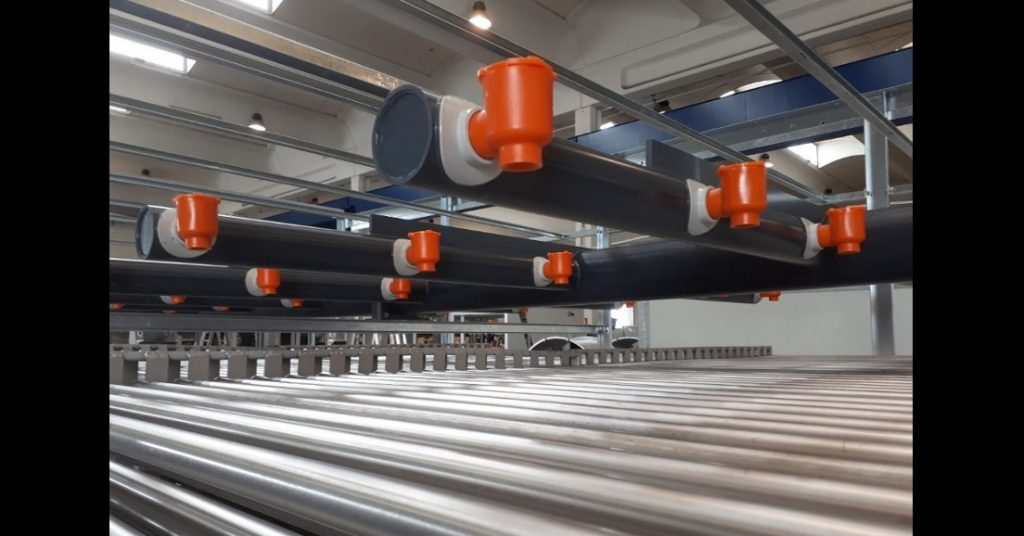
2.2. Components of cooling towers and the materials used
Now we come to the main components that characterise evaporative cooling towers, whether open or closed circuit.
- Principal containment and support structure for the evaporative tower: this can be made of sheet metal, fibreglass or both materials. For extremely large industrial or hyperbolic towers, cement is also used.
- Heat exchange surface (in open circuit towers) or heat exchange coil, generally with bundles of smooth tubes (in closed circuit towers): these are the “heart” of the evaporative tower. In fact, these are the components through which the heat exchange between water and air takes place.
- Axial or centrifugal fans: this is the only moving mechanical part and is the component that “forces” the water evaporation required to achieve cooling. The choice of an axial or centrifugal fan, depending on the design conditions, is important in order to achieve the most efficient operation and the lowest energy use of the system. Let’s look at the criteria.
- Water distribution system, normally consists of ramp of pipes and nozzles. It makes it possible to distribute the water to be cooled over the heat exchange surface (open circuit cooling towers) or on the heat exchange coil (closed circuit cooling towers).
Droplet eliminator, located immediately upstream of the fan. It serves to retain the water droplets, which would otherwise be carried outside by the flow of air caused by the fan.
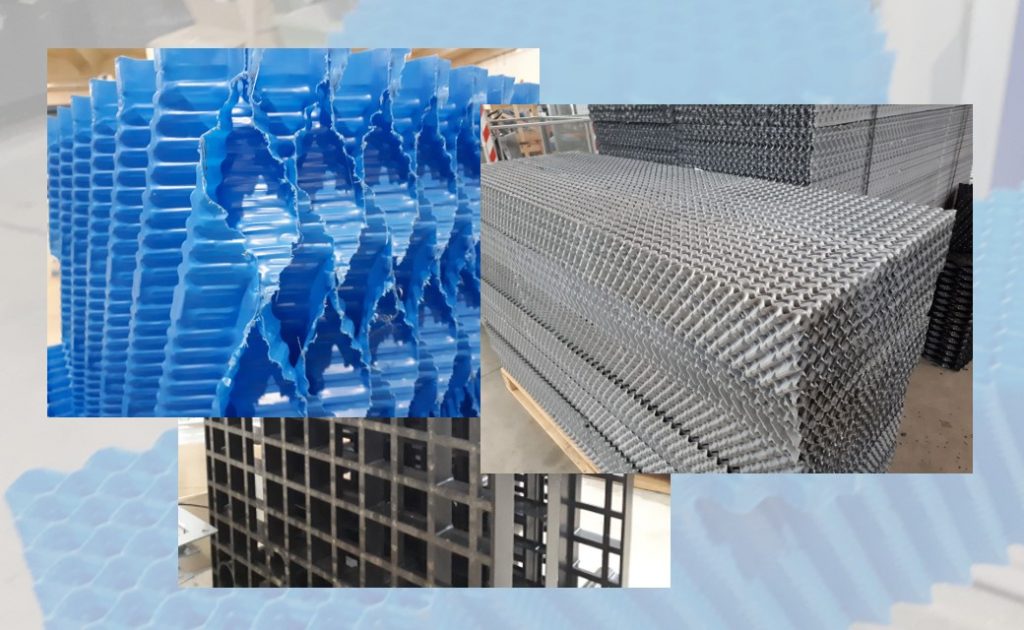
Furthermore, the nature of the water to be cooled greatly influences both the choice of the construction materials to be used, as mentioned above, as well as the most suitable type of heat exchange surface. For water which is particularly aggressive or acidic, corrosion-resistant materials or fibreglass would be the preferred choice, the latter being inherently unaffected by most chemical agents.
On the other hand, if the water could be polluted by the process, dragging with it turbidity or other pollutants, including those of an organic nature, the most suitable type of heat exchange surface must be assessed from those available: from antifouling, to vertical non-crossing channels, to the classic “splash” packs which are based on the principle of droplet separation.
2.3. Bleed-off and make-up
As mentioned above, evaporative towers achieve their purpose of cooling water by the forced evaporation of a determined amount of water. The quantity of evaporated water is directly proportional to the amount of heat to be dissipated: more specifically, approximately 1 litre of water is lost for every 600 Kcal of thermal load which is dissipated.
This is an incontrovertible fact of physics and represents one of the few “critical” aspects which therefore must be managed, in the clearly positive balance of evaporative systems compared to other cooling technologies.
To achieve cooling, the evaporated water must be reintegrated into the circuit: it is good for this to be carried out by conditioning the water quality in such a way that scale deposits and deposits in general do not occur within the circuit. This is because the concentration of salts contained in the evaporating water are dissolved in the remaining water, slowly increasing in concentration. In short, it is essential to control this concentration and ensure certain limits are not exceeded: normally, a suitable limescale treatment and the partial bleed-off of water contained in the circuit are more than adequate for this purpose.
While the evaporated water is a function of the dissipated heat and cannot therefore be modified in quantitative terms, the water that is defined as “bleed-off” can be modified and serves to maintain the quantity of dissolved salts within certain limits.
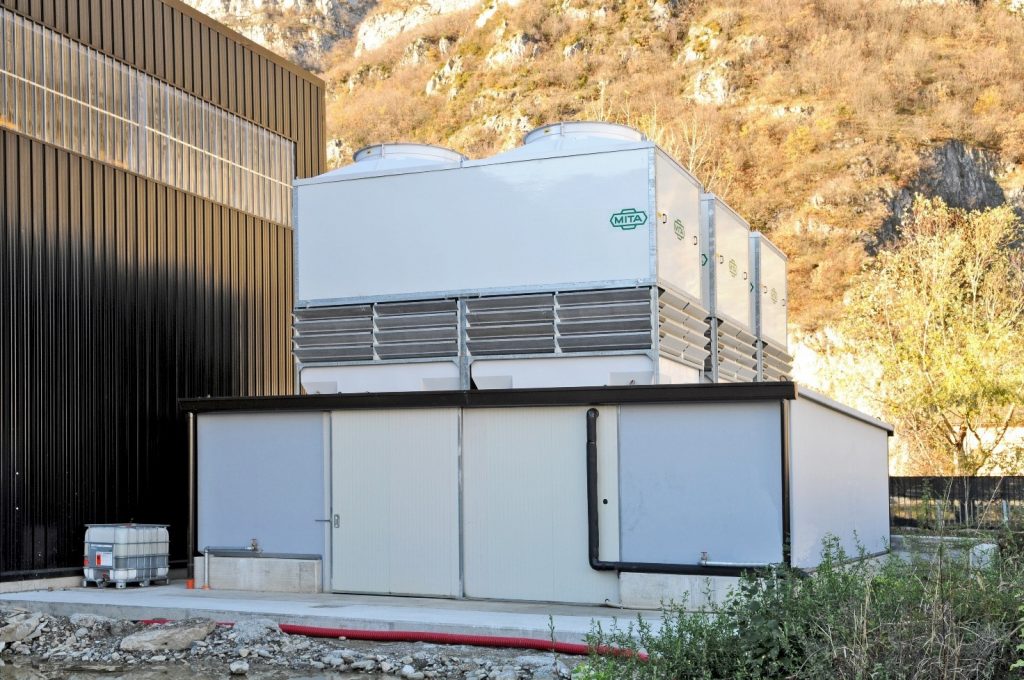
The bleed-off can be managed “empirically”, tending towards being the same as the evaporate (concentration factor of “2”). Or it can also be controlled by continuous monitoring of the quality of the water contained in the circuit, especially the electrical conductivity parameter.
Controlling conductivity by means of special limescale treatments and then managing the bleed-off appropriately makes it possible reduce the amount of water which is wasted. Not only that, it also allows the efficiency of the system to be perfectly maintained and increases intervals between maintenance interventions and the replacement of components subject to wear. Therefore, the ideal solution may be to select an “integrated” system for your facility, i.e. packages that, in addition to a single evaporative unit, also include specific equipment to control and manage the water. Better still, if proposed directly by the Manufacturer: this way they may be suitable in terms of materials and specifically designed for the machine it serves.
Ask for information3. Cooling towers: main industrial and civil applications
As explained at the beginning, evaporative cooling towers are widely used in the following types of plants:
- energy production;
- air conditioning of public buildings;
- refrigeration;
- industrial;
This last area certainly represents the sector which most frequently uses evaporative towers, above all for medium and high power plants.
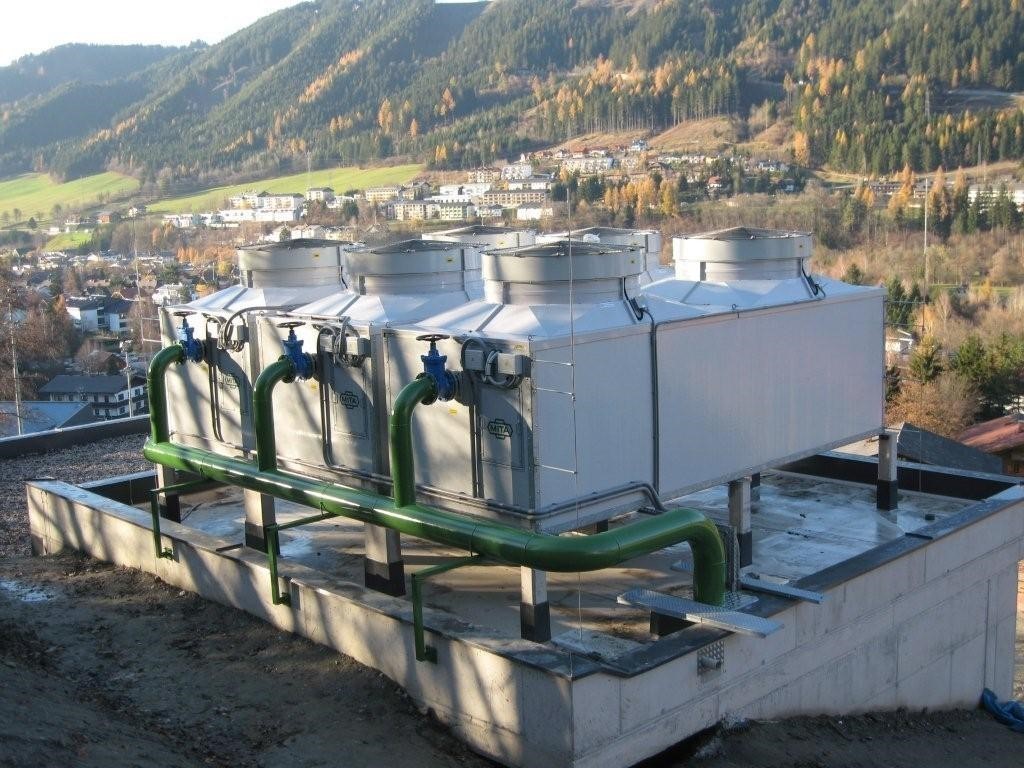
3.1. Evaporative cooling towers: the optimal solution for higher levels of power
All other cooling systems, whether they involve air, adiabatic or refrigeration units, represent a possible alternative when the thermal power to be dissipated is relatively modest, below 1 MW as a reference. However, they become extremely uneconomical when it comes to significantly high power, even several MW.
In the industrial field, both open-circuit and closed-circuit cooling towers are used: in the latter instance, the fluid to be cooled (water or a mixture of water and glycol) circulates inside a coil made of smooth pipes. In turn, this is externally wetted and the forcibly evaporated water dissipates heat to the internal fluid.
3.2. Cooling towers in combination with heat exchangers
Closed circuit evaporative towers are a valid alternative where “indirect” cooling of the user is to be performed: namely, where the liquid in the cooling circuit is not polluted by the air.
The same type of indirect cooling can be achieved with an open circuit evaporative tower in combination with either a plate heat exchanger or a tube bundle heat exchanger. The advantage of the former system is that both the evaporative section and the tube bundle heat exchanger can be found in a single machine: the advantages in terms of the space occupied and costs are unquestionable.
3.3. Cooling towers combined with condensers of water-cooled chillers
Evaporative cooling towers are also used in HVAC sector and, above all, all industrial and commercial refrigeration: in particular, together with the condenser of water-cooled chillers, today more than ever in absorption units.
3.4. Examples of the application sectors
Lastly, and by way of example, here is a list of industrial or civil application sectors in which cooling towers can fulfil their purpose of dispersing process heat.
- Nuclear, thermal, geothermal and coal-fired power stations.
- Oil & Gas plants: large industrial cooling towers are often used
- Refineries
- Production of plastics and heat treatments of metals (such as steel mills and foundries).
- Cogeneration and trigeneration
- Air conditioning systems in civil and industrial buildings (HVAC).
- Supermarkets together with chillers.
- Small production systems such as ice-cream parlours.
4. Types of evaporative cooling towers
We now come to the different types and construction variants of cooling towers: during the design phase, the choice is based on the application for which they are intended, or on the size of the plant.
The most frequent variables which can affect the choice are mainly the following:
- thermal power to be dissipated,
- nature of the water to be cooled,
- process type,
- context within which installation takes place (civil or industrial),
- particular plant requirements, for example, if it is a new system or a replacement.
4.1. Field-erected and factory-assembled cooling towers
The size of the system (in terms of thermal power to be dissipated) directs the choice towards two systems: “package” type evaporative cooling towers, namely pre-assembled at the factory, or “field-erected“ (erected directly on site).
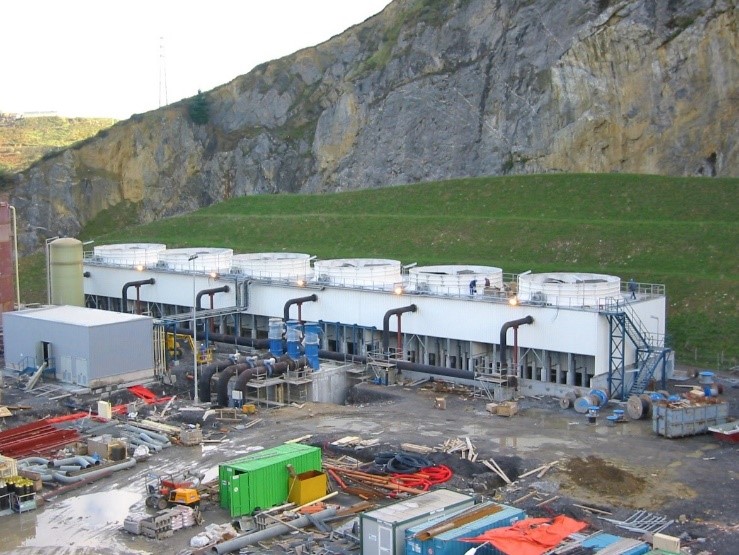
The former can be made both in metal and in other materials that are “less sensitive” to the presence of water and its possible corrosion effect: for example fiberglass. The latter are generally made with a metal structure or with pultruded profiles in fiberglass, if not actually in concrete: the classic hyperbolic towers of nuclear power plants.
4.2. Standard or silent solutions
Another element that influences the choice of the most suitable construction solution is the installation area: if we talk about the HVAC sector (hospitals, shopping centres, air conditioning systems), a solution with a low acoustic impact is preferable. A machine constructively designed to have low noise emissions or in any case easily silenced should therefore be chosen.
If the area of installation is industrial, the noise limits, although present as a project request, are certainly less binding and a less specific solution can therefore be proposed.
4.3. Are centrifugal or axial fans preferable?
To answer this question, let’s take a step back in time.
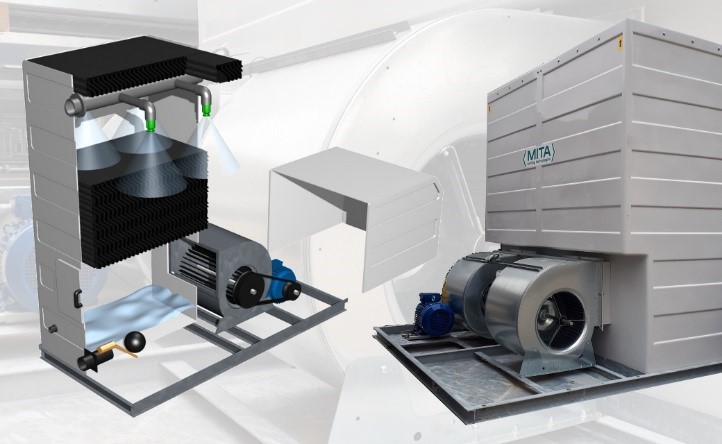
In the past, there was a tendency to direct the choice in the civil sector towards evaporative towers with centrifugal fans. Axial fans were preferred when it came to industrial processes.
Today there are evaporative cooling towers with axial fans which are as efficient as they are silent, to the point that this difference is no longer so clear. This is explained in this article on centrifugal-fan and axial-fan cooling towers.
4.4. The right solution for the right plant: gathering information
Lastly, it is also important to know any dimensional limits or limits related to other pre-existing situations that can lead to one choice or another being preferable.
For example, in the case of a replacement, there may be an existing basin or a space defined by the previous installation which needs to be considered. However, it is less common to find a limit of this nature, or it can be identified from an area within which the cooling system is intended.
All these aspects must be discussed during the data collection phase between the Customer and the Supplier, with the Supplier responsible for assuming a “consultancy” role on cooling for the Customer so that the proposal can be the best from both a technical and an economic point of view.
Ask more information5. Water treatment and maintenance
Like all devices within a technological system, evaporative towers, of whatever type, also require a routine maintenance programme and, in the event of a failure, an extraordinary maintenance program.
Because of the extreme simplicity of construction, cooling towers do not require particular attention, apart from the observance of some very simple and effective guidelines to ensure they are always kept in optimum operating conditions.
In fact, safety and efficiency go hand in hand.
5.1. Tower water treatment
The most delicate aspects are certainly attributable to the nature of the circulating water: namely, not only attention to the type of water to be cooled, but how this water is controlled and conditioned so that it does not deteriorate from a physical-chemical point of view.
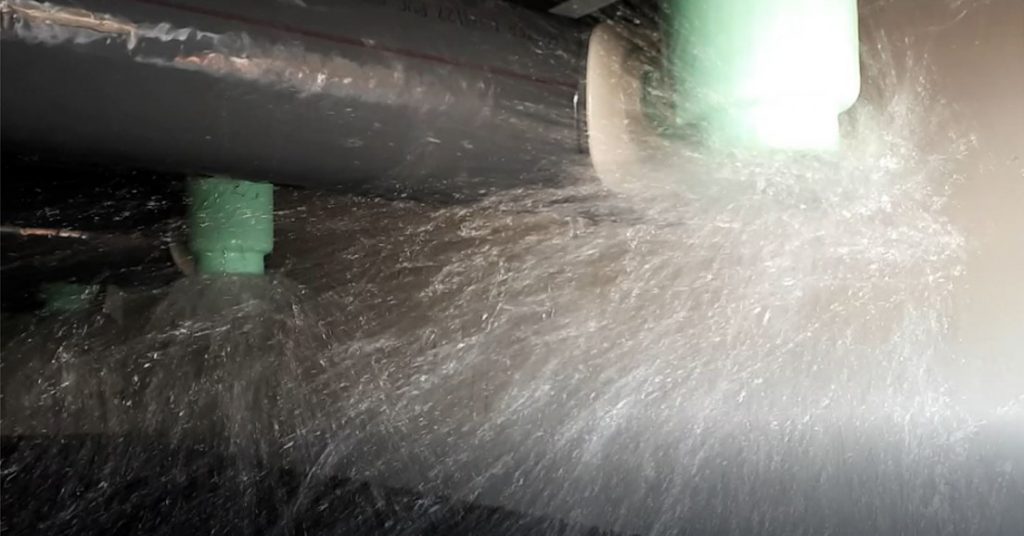
Well-treated water, avoiding scale deposits and other deposits in the evaporative tower and in the plant, also has a great positive influence in minimising the possible proliferation and diffusion of organic substances (algae) or bacteria, including the most common and potentially dangerous one which can cause Legionella.
A clean evaporative cooling tower means an evaporative tower which is always efficient, therefore able to offer maximum efficiency with minimum resourse use, both in terms of electricity and evaporated and purged water.
5.2. Good practices provided by a tower manufacturer
Obviously, the components that make up the evaporative tower also benefit from correct management: the heat exchange surfaces have a longer life, just as the motors and fans work in better conditions thanks to the less aggressive water that can cause a deterioration of the most sensitive parts.
With regard to the practices to be followed to obtain this condition, it is generally sufficient to comply with the specific indications provided by the Manufacturer regarding periodic checks and maintenance, as well as the physical-chemical parameters to be observed for the water in circulation. However, there are more general guidelines, often also mentioned in the Manufacturer’s manuals, which provide “good practices” valid for all systems where evaporative towers are used: prestigious bodies in this sense include Cooling Technology Institute and Assoclima (Confindustria).
These are useful impartial suggestions for optimal running of the entire system.
Find out about good evaporative cooling management practicesResources
Best practices
Read all Pieces of Advice by MITA Cooling TechnologiesWhat to Know
Find Out All Technical TermsTechnical Articles
Read All our Technical ArticlesNewsletter
Subscribe to MITA newsletter and stay updated on technical solutions for industrial and civil cooling and get to know our offer.