Service
MITA is with you before, after and during installationThere is no technical solution without customer service and cooling technologies are no exception: this is why MITA Service will always be at your side.

Maintenance Technicians
Ordinary, extraordinary or predictive maintenance is not a problem anymore: nor in evaporative cooling towers nor in adiabatic coolers. Just rely on an advisor reminding you of the deadlines and taking care of your plant’s efficiency and safety.
Go to the PageInspection Visits to the Cooler
MITA Service team can always be contacted for inspections once the plant has started up. You can count on an immediate operative diagnosis thanks to easy access to the internal parts of the unit.
Go to the Page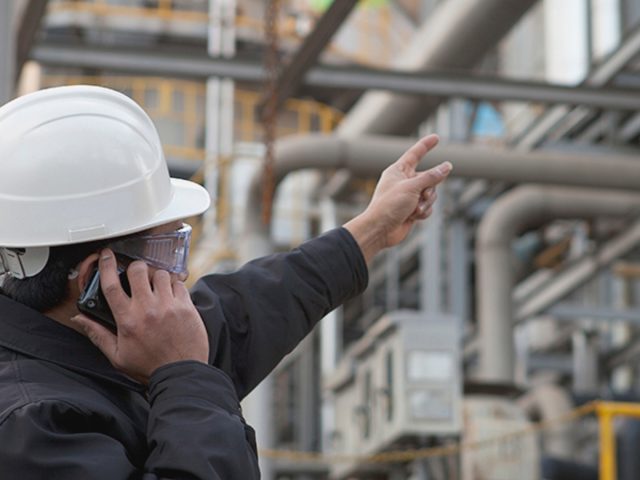
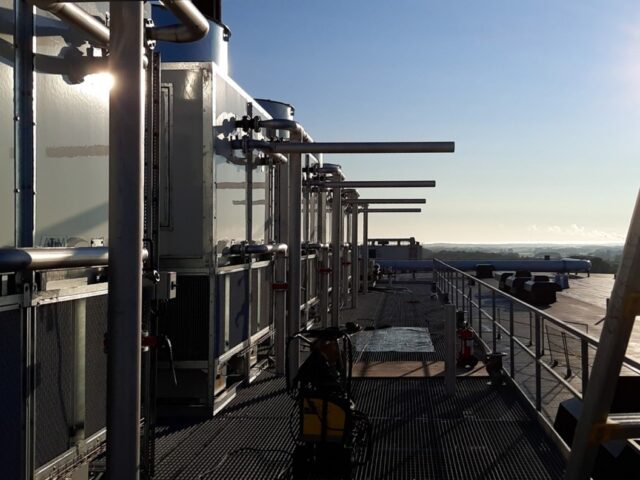
Cooling Tower Protection
The cooling towers of MITA Cooling Technologies are made of long-lasting materials: fibreglass, PP and PVC, hot-dip galvanized steel. Furthermore, the customer can choose C-Protection Coating: an additional protection of hot-dip galvanized steel parts.
Go to the PageRemote Management Service
Your cooler already has its own remote management platform installed: the next step is to commit MITA Service team to run it. You will always be aware of the performances of your equipment, scheduling ordinary and extraordinary maintenance in advance.
Go to the Page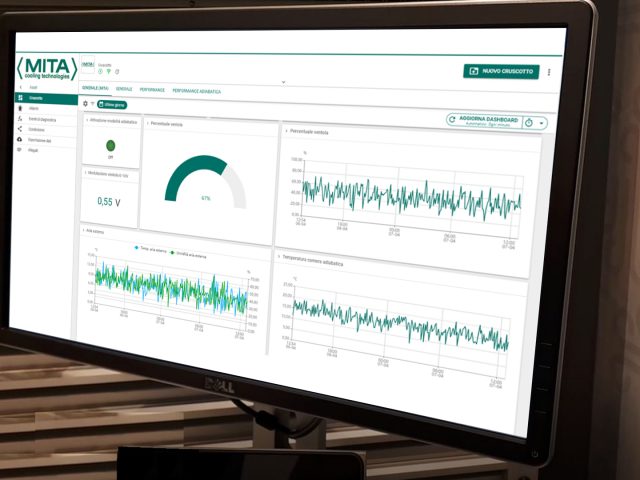
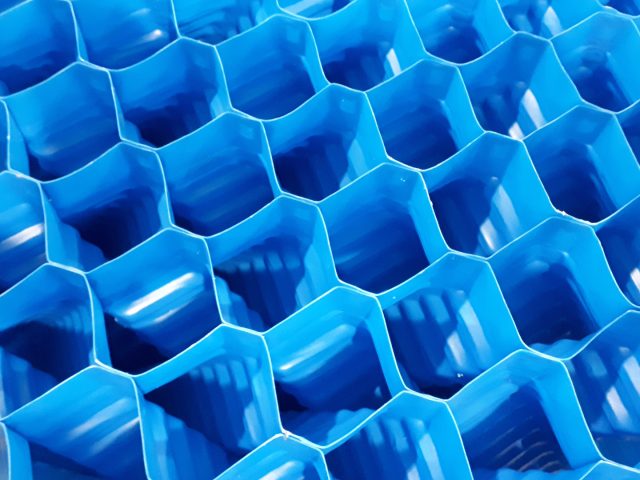
Spare Parts
It is important to keep the cooler at maximum efficiency to save energy and management time. MITA offers wide spare part sets for cooling towers and for other industrial coolers.
Go to the PageMITA Service at a Glance
- Assistance during handling and installation: support by qualified technicians for operations such as handling and/or positioning of the machine.
- Start-up assistance: qualified technicians for possible assistance with all the start-up operations to ensure perfect functioning and check the main parameters (absorption and pressures of the circuit).
- Cleaning and sanitisation of the machine.
- Extended warranty: for parts not subject to normal wear, there will be an extension of 24 months from the standard warranty end date.
- Original spare-parts, set for the first 5 years of operation: at an attractive price, always with the certainty of immediate availability.
- Scheduled maintenance: checks completed in due time, to ensure the efficient cooling, perfect functionality and maximum productivity of your plant, especially on the hottest days.
- Courses and technical training: staff training courses to learn how to properly service and operate the machine.
Resources
Best practices
Read all Pieces of Advice by MITA Cooling TechnologiesWhat to Know
Find Out All Technical TermsTechnical Articles
Read All our Technical ArticlesTools to help you choose
Preliminary plant evaluation
Tailor-made design
Newsletter
Subscribe to MITA newsletter and stay updated on technical solutions for industrial and civil cooling and get to know our offer.