Examples of processes: Injection molding, extrusion, rubber processing, bioplastic industry.
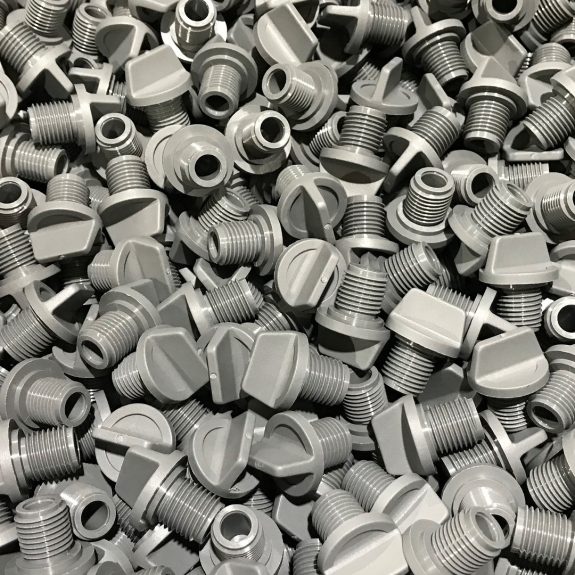
Cooling Systems for Plastic and Rubber Processing
Plastic and rubber processing requires specific cooling processes to ensure high productivity, finished product quality and temperature control during molding, extrusion and mixing. MITA Cooling Technologies offers advanced solutions-from chillers to adiabatic cooling systems-that optimize the cooling of molds, hydraulic components and oils, ensuring reliability and energy savings.
Typical needs: Precise temperature control, cycle time reduction, energy efficiency.
Technologies offered: chiller industriali, torri evaporative, dry cooler adiabatici.
1. Typical needs of the industry
The plastics and rubber industry requires continuous and stable cooling to maintain product quality and integrity during production processes. Key requirements include:
- Precise temperature control: essential to avoid material deformation and shrinkage.
- Energy efficiency and sustainability: reduced water and energy use and low environmental impact.
- Operational reliability: machinery in continuous operation, with low maintenance requirements.
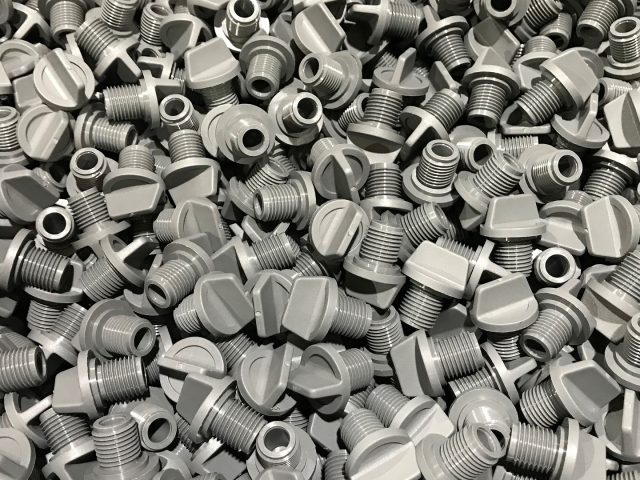
2. MITA Cooling Technologies' solutions for the plastics industry
MITA Cooling Technologies offers tailored solutions to meet the needs of the plastics and rubber industry.
- Industrial process chillers: for high-efficiency cooling of molds and processes, with very low outlet fluid temperatures.
- Adiabatic dry coolers: solutions that take advantage of adiabatic cooling, ideal for sustainability and water-saving needs.
- Cooling towers: systems with high efficiency through the use of water.
MITA’s systems can be equipped with remote control for centralized and timely management, facilitating predictive maintenance interventions.
3. Examples of industry processes served by cooling technology
Speaking of cooling in plastic and rubber processing, we deal with processes that are heterogeneous with each other. Thus, here are three examples.
- Plastic injection molding: fast cooling of plastic molds and components to increase productivity and prevent deformation.
- Rubber and plastic extrusion: temperature control for uniform, defect-free processing.
- Bioplastics industry: customized solutions for environmentally sustainable materials with specific temperature and environmental control needs.
4. Focus: cooling technologies for plastics molding
Molding is a typical example of a case where cooling technologies can be applied to plastic processing.
Plastic molding machines are equipped in a granule tank for the raw material from which the part is to be made. The granule is heated and melted, before being pressurized into the mold.
The mold is usually fully automatic, so that the opening and ejection of the part takes place without manual intervention. Inside the mold are channels that are used to cool the mold itself and, more importantly, the molded part: for this cooling, a refrigeration unit is usually required since the water temperature must be very low in order to allow for fast cooling (to avoid material shrinkage and to allow for higher productivity).
Injection of the molten plastic material into the mold is accomplished by an oil hydraulic system, for which pumps are used that need to be cooled with water.
The use of the evaporative cooling tower, or other cooling technology, is possible for this section of the process: in fact, we are talking about simple heat dissipation for which no particularly low temperatures are needed.
Ask for InformationMITA Cooling Solutions for Plastics and Rubber
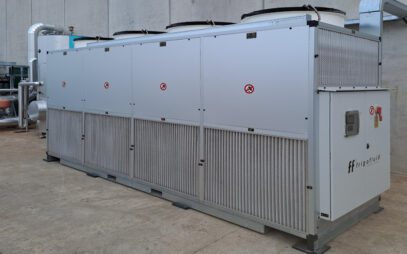
RW / EFC ax Chiller with Free-Cooling
The RW / EFC ax chiller combines energy efficiency and sustainability for industrial refrigeration with integrated free-cooling technology. The combination of operating modes, between free-cooling and compressor operation, allows up to 80 percent energy savings compared to conventional versions.
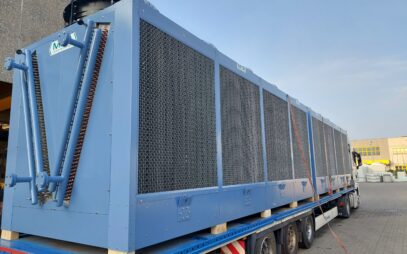
PAD-XL W Adiabatic Cooler
Ideal for those who want to use very little cooling water while eliminating its management, or as an alternative to the classic dry cooler, especially with performance in the hottest times of the year in mind.
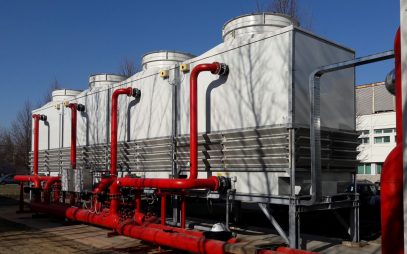
PME-E Open-Circuit Evaporative Cooling Tower
A light and non-corrodible open-circuit evaporative cooling tower: process industry and HVAC operators will be able to count on its multiple versions and ease of transport and installation.
Some MITA achievements for the plastic and rubber industry
Cooler Replacement for a Manufacturer of Porcelain Products in the Netherlands
Significant water savings and a wide range of available solutions-these two factors were key for a Dutch manufacturing company replacing its cooling systems. Two adiabatic dry coolers from MITA Cooling Technologies.
Learn MoreExtraordinary water savings for the plastics industry with the MITA adiabatic system
A plastics processing company in the province of Lecco has chosen the PAD-V cooler for the cooling circuit of its production plant: the eco-sustainable system that cuts water and energy bills.
Learn MoreYour Plant Needs
Tools to help you choose
Cooling Advisors
Preliminary plant evaluation
Tailor-made design
Resources
Best practices
Read all Pieces of Advice by MITA Cooling TechnologiesWhat to Know
Find Out All Technical TermsTechnical Articles
Read All our Technical ArticlesNewsletter
Subscribe to MITA newsletter and stay updated on technical solutions for industrial and civil cooling and get to know our offer.